Digital Solution and Service Portfolio Innovation
Digital Solution and Service Portfolio Innovation
To innovate the service portfolio and develop new digital solutions, co-creation is the perfect approach to combine our consulting expertise with the broad knowledge within the organizations of our clients. This is the basis for the development of a portfolio meeting market and customer needs. In addition, completely new portfolio elements with high market potential can be developed.
- Analysis of market needs and definition of innovation fields
- Ideation and prioritization based on co-creation
- Definition of the roadmap and agile implementation plan
- Innovative portfolio meets customer demands with greater effectiveness
- Reduced time-to-market for new solutions based on the co-creating approach
- Improved customer satisfaction due to even more attractive solutions
- Openness for an innovative approach (e.g., co-creation)
- Availability of experts for the co-creation approach
- Support of management
Our industry leaders
Customer-centric Transformation & Strategy
Customer-centric Transformation and Strategy
The Customer-centric Transformation and Strategy focus on defining a customer-centric business model and a transformation process to support the Customer Centric Strategy. The result is a shift from a product-oriented to a customer-oriented value chain.
- Customer experience framework as a definition of a customer-centric business model
- Business model canvas and business case to ensure sustainable success
- Transformation plan as the basis for a smooth transition of the business model
- Improved customer relations through better customer satisfaction
- New revenue streams based on a redefined business model
- New value pools by leveraging customer insights
- Reduced time to market based on better efficiency
- Resilience by directly addressing customer needs
- Defined Customer Interaction Strategy
- Willingness to redefine the existing business model
- Availability of key experts and support of management
Our industry leaders
Customer Interaction Strategy
Customer Interaction Strategy
How to design unique customer interactions? How to define the right channel and touchpoint setup? How to integrate physical and digital channels and touchpoints? These are some of the main questions that must be answered within a Customer Interaction Strategy.
- Digitalization and connection of customer touchpoints in one learning system
- Creation of reach, optimization of the sales funnel, and expansion of the brand's ecosystem
- Continuous improvement through analytics-based automation and innovation
- Improvement of customer retention rate through an increase in conquest and retention
- Improvement of NPS based on superior customer experiences
- More revenue per sale based on optimized sales and marketing performance
- Availability of data and access to relevant experts
- Support of top management
Our industry leader
Cybersecurity Risk Assessment
Cybersecurity Risk Assessment
Capture cyber landscape, analyze critical risks and define concrete mitigation plan
Siemens Advanta’s holistic risk management strategy revolves around our clients' core goals, empowering them to thrive in an era of escalating uncertainties.
Siemens Advanta helps identify and prioritize risks according to their business impact and derives tailored measures to proactively manage them for its clients. Siemens Advanta’s management perspective helps its clients minimize risks effectively and achieve faster responses through prioritized actions, better risk mitigation, and increased risk coverage by linking IT, OT, and Cloud environments.
From embracing a comprehensive approach to managing risks, Siemens Advanta centers its strategy around the fundamental goals of its clients, leveraging globally recognized cybersecurity practices. This ensures heightened cybersecurity and cyber resilience in an increasingly uncertain world.
Siemens Advanta provides a step-by-step approach to capture an organization’s cybersecurity landscape in four main areas: governance, people, process, and technology. Risks are identified and prioritized according to their business impact and the likelihood of a cybersecurity incident. Finally, Siemens Advanta tailors and defines concrete measures, responding directly to the unique needs of its clients.
Siemens Advanta’s management perspective enables its clients to act swiftly, focus on high-priority tasks, improve risk mitigation, and increase risk coverage by linking IT, OT, and Cloud.
- Identification of qualitative and quantitative cybersecurity risks
- Analysis and prioritization of identified risks based on likelihood and impact
- Defining security controls and implementing measures to achieve targeted security levels
- Strengthened resilience against unforeseen challenges and risks
- Enhanced agility when adapting to changing market conditions and improved resource allocation for effective risk management
- A customized risk assessment methodology tailored to the company's unique needs and objectives
- Increased shareholder value through prioritizing high-impact risks and mitigation actions
- Expanded risk coverage by connecting IT, OT, and Cloud systems
- Establishment of key business goals by senior management
- Access to essential data, such as IT infrastructure, data assets, and existing security controls
Our industry leader
Data Strategy
Data Strategy
Our Enterprise Data Strategy solution enables organizations to capitalize fully on their data assets. We assess the data strategy maturity of industrial enterprises, identify infrastructure requirements, develop employee competencies, and advocate for ethical data use. With our robust enterprise data readiness assessment framework, we pinpoint capabilities across data-centric business, people and processes, and tools & infrastructure, helping clients shape and execute their data strategy based on priority areas.
- A well-defined roadmap and sustained support for implementing recommended data strategy initiatives and realizing set goals and objectives
- Seamlessly integrating data initiatives with overarching business objectives in a data-centric business approach
- Fostering a data-centric culture and cultivating a data-literate workforce
- Streamlining data collection and deploying data-enabling tools & IT architecture
- Achieving a comprehensive data maturity assessment, showcasing strengths and opportunities for growth
- Focused attention on high-impact data strategy initiatives to deliver transformative outcomes
Our industry leader
Sustainability Check-up
Sustainability Check-Up
Quickly assessing a firm's sustainability maturity is essential in the jungle of increasing customer requests and constantly changing regulations. Companies need to understand where they are on their sustainability journey. Siemens Advanta's Sustainability Check-up is a quick two-week assessment of a company's maturity level. It accelerates their sustainability transformation through concrete recommendations to tackle future challenges.
- Receive a unique sustainability maturity profile, with an overarching ESG score across 16 categories
- Get best-in-class insights accompanied by tailored recommendations and concrete next steps
Our industry leader
Custom Solutions
Custom Solutions
Design & development of custom solutions
Digitally transforming by, for example, incorporating IoT into an enterprise is a complex process that requires many calculated decisions. Siemens Advanta can define, design, and implement solutions to tackle today’s evolving challenges and meet emerging business requirements. Implementing the right solution architecture is key to economic progress with a comprehensive outlook, ensuring the best tools to solve unique business needs.
- Consulting and Integration
- Reduced risk and complexity
- Holistic, tailored end-to-end solutions
Our industry leader
How Digital Twins Deliver the Holy Grail of Connected Supply Chains
Building Resilience: How Digital Twins Deliver the Holy Grail of Connected Supply Chains
Listen to the blog here:
For CEOs of industrial manufacturing firms, one of the biggest concerns arising from the COVID-19 pandemic has been supply chain disruption. One study put the average cost to large businesses (those with revenues above USD 1bn) at around USD 184m in 2021.
Throughout 2020, the number of organizations experiencing 20 or more supply chain disruptions increased by a factor of six, according to the Business Continuity Institute’s 2021 Supply Chain Resilience report. This ranged from the Suez Canal blockage to container pileups in Shanghai and other major ports. If this wasn’t enough, ongoing climate change issues as well as geopolitical changes were the missing cherry on top. The same report found that the proportion of senior management showing a medium or high commitment to supply chain risk rose by nearly 10 percent to 82.7%. This goes to show that these global influences have the effect of transforming supply chains into revenue assurance drivers rather than cost reduction pillars.
Faced with this increasing volatility, uncertainty, complexity and ambiguity, the number one priority for sector leaders is to build resilience into the supply chain. Due to the pandemic leaders’ priorities shifting to business continuity and their realization that connectivity is the golden ticket, the challenge lies in a successful way to accomplish this.
The Holy Grail – connectivity across the supply chain
The global supply chain market is expected to experience a compound annual growth rate of 11.2% from 2020 to 2027 – a market value surge from USD 15bn to USD 37bn. With the added speed bump of supply chain disruptions, it’s time to build resilience into your supply chain, and business leaders are reaching for plentiful and readily available technological developments to do so. Currently, the IIoT-based solution showing the most potential when creating a resilient supply chain is the use of digital twins to mimic supply chains and productivity networks.
In recent years, the digital transformation of supply chains has made them increasingly dynamic and complex. Catalyzed by the pandemic and other previously mentioned supply chain hurdles, manufacturers have sought out new ways to optimize supply chains to ensure transparency. To do so, in-depth understanding and visibility of the entire end-to-end ecosystem of suppliers and customers – their needs, strengths, weaknesses and potential risk factors – is the Holy Grail.
This ideal of a fully connected ecosystem providing real-time data starts by connecting your own supply chain. Only once you have complete visibility of your own end-to-end operations, connection with the wider ecosystem can be achieved, enabling you to create a holistic overview and transparency from customer to supplier.
Based on this holistic overview, you need to decide on your own business goals and adjust your digitalization strategy accordingly. Easier said than done? Not necessarily. The important thing is not to drown in the ocean of possibilities and to keep your eye on your business goals, letting them dictate the level of detail your digital solution requires.
Digital twins – the kick starter for connected supply chains
It’s estimated that up to 93% of all IoT Platforms will contain some form of digital twin capability by 2027. So what exactly is a digital twin? And how does it tie in with a connected supply chain? To put it simply, a digital twin is a virtual representation of a physical product or process. By feeding it with data, it can be used to model the current situation in real time, test ‘what if’-scenarios for the future and, in some instances, even provide ‘best practice’ to the modelled disruption. As such, it provides predictive insights, highlights areas of weakness or potential failure and enables timely preventative action.
By incorporating the latest technical innovations (eg multi-physics simulation, AI, data analytics and machine learning), digital twins can demonstrate the impact of usage scenarios, environmental conditions and other variables to improve the resilience of a supply chain. The digital twin is therefore the ultimate goal in connecting your supply chain, yet you need to learn to walk before you can run. Start by determining the digital journey most adequate for reaching your business' set goals and drivers. Luckily, there are a few maturity levels you can reach before chasing the Holy Grail of the digital twin, and there is likely a data solution for every organization and budget.
To provide visibility and transparency on an operational level, applying a digital map or model might suffice, as it provides basic insights into your operations. However, if you want to leverage data to simulate and explore various possible scenarios and the effects of changes before implementing them in the physical supply chain, a digital shadow might be the best approach. However, only a digital twin can create enough insights to enable real-time connection and provide concrete simulations for operational, tactical as well as strategic decision making.
How to implement a digital twin fit for your goals
The key to realizing this ideal scenario is leveraging the correct data in the correct way by the correct people. However, as with any form of digitalization, there are several factors to consider when starting the journey to executing a digital twin.
Firstly, it’s crucial to always have your goals in mind: the business outcome you want to achieve should be the foundation for your decision as to which data model to use. For certain organizations, it may not be necessary to apply an end-to-end digital twin at the very beginning of your digital transformation journey. Trying to navigate through the buzzwords and promises from solution providers and staying true to your core needs is therefore an important first consideration. Applying technology just for the sake of applying technology is never the solution!
Secondly, a digital twin is only as good as the data it gets fed. Therefore, you need to gather useful data and that’s the tricky part. When creating the digital twin, connecting your internal data is advised, as this is the data that’s readily available to you. However, it’s important not to fall into the trap of data overload, which can result in too many insights slowing down and clouding the decision-making process. Once you have an internal connected supply chain in place, you can start reaching out to your ecosystem to further increase connectivity. It’s essential to take the time to understand relevant data management solutions for your business goals and ecosystem.
Everybody knows that data is the new gold in business, and companies are often reluctant to give it up lightly. This results in a potentially complex process of connecting your full ecosystem, as you need to convince all stakeholders about the joint value that can be created through sharing knowledge and creating transparency. As soon as they’re fully connected and sharing their data, you can collectively create the most detailed digital model possible, which will benefit everybody along the chain.
However, in reality it’s unlikely that every member of your ecosystem will share the data needed to simulate a complete supply chain digital twin, but that does not mean the end of the line for your digital twin journey. The good news is that there is a sophisticated workaround to help you overcome this particular roadblock: artificial intelligence (AI). Through AI, it’s possible to model the missing data and thus fill in gaps in your data lake. Furthermore, other data sources can be fed into AI to derive expected impacts to the supply chain from striking events, for example the news of a flooding in a particular region in the world can be overlaid with your supplier base and the digital twin can preempt potential impacts and solutions.
Everybody knows that data is the new gold in business, and companies are often reluctant to give it up lightly.
Making the process match the insight
Now that your data is in place and connected, the true benefit of a digital twin emerges. Real time connection and seamless data flow will enable direct transparency of your data, and customized visualization, dashboards and alerts will allow for rapid decision making. The only question is, will your decision-making processes be able to keep up with this increased speed of knowledge?
Data digitalization and process optimization need to be harmonized, as data without a process is useless, and a process without data is inefficient. Future supply chains will be a combined learning network of humans and technology, so alongside building your digital twin, it’s important to invest in the creation of a flexible workforce willing to adapt its skillset to facilitate a bionic supply chain. After all, the most powerful intelligent network is still the human mind, and it’s fundamental in deriving and acting on the benefits of a supply chain digital twin.
Enabling and benefitting from the factor of the future
When applying connected supply chains in the industrial manufacturing environment, it is important to shed light on how their connection to the green, lean, and digital factories of the future will look like. In this specific context, the successful creation of supply chain digital twins depends on the quality of data from every factory, warehouse, or nod within the supply network. This means that it is best practice to successfully develop digital twins of your factory in the first place. This will make the trick for the whole network as data could be provided seamlessly.
At the same time, it is crucial to understand that the factory of the future and its successful operations heavily depend on seamless data flows, processes, connectivity, and agility on a large scale in order to ensure individual productivity, robustness, and delivery excellence. Ever changing markets, customer requirements and supply disruption can only be managed sustainably by building agility and reactiveness into the mix. The supply chain digital twin can be the dealmaker in this context enabling the transparency needed beyond one’s own facilities. In the end, the factory of the future, being green, lean and digital in nature, is both enabler and benefactor from the creation of a supply chain digital twin. Seamlessly, connected supply chain can build the basis for factories and whole networks to decarbonize operations.
Unlocking the potential of supply chain digital twins
Increased connection and digitization open the possibility of creating supply chain digital twins, but it’s not actually the digital twin that creates the value for your business. A digital twin is simply the vehicle you need to enable a fully connected supply chain, and the strategic connection with your individual business goals is the key that makes your vehicle perform. As a result, your entire ecosystem will gain a competitive advantage.
Siemens Digital Industries Logistics (DI LOG) has already paved the way towards a comprehensive digital supply chain twin with their end-to-end resilience solution. This platform helps both Siemens and its partners to proactively manage supply chain and operations based on real time tracking and data-driven alerting functionalities for all involved parties within the network.
Free whitepaper
Based on our unique experience in digital factory environments, we identified several company as well as use case specific factors to make the groundbreaking decision between edge and cloud. Download our whitepaper and learn which factors to consider when unlocking the full potential of your IIoT journey!
Our experts
Author
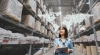
Green – Lean – Digital: The Factory of the Future
Green – Lean – Digital: The Factory of the Future
Listen to the blog here:
In the discrete manufacturing, plant engineering, food & beverage, and automotive sectors, applying lean principles and automation has been and will remain evergreen when striving for efficiency gains. The golden rule appears to be: the more efficient and flexible the manufacturing processes are, the more profitable and competitive a company will be. Holding true, keeping your processes as lean as possible will build the foundation for the factory of the future, but the best process is still the one that doesn’t exist. The next big milestone on the path towards efficiency and flexibility is digitalization. Production companies already started transitioning from analog to digital information as well as collecting and connecting data throughout the value chain. Through digitalization, production complexity becomes manageable, behavior of machines and assets predictable, disturbances in supply chains transparent, production systems quickly adaptable and as a result, productivity overall rises.
However, the growing importance of sustainability as well as decarbonization of supply chains and own operations is adding additional requirements and challenges for the digital transformation of factories. There is a new goal to reach now that making production sustainable is no longer an option – it’s a must. Once your factory is lean and digital, what does it take to make it green as well? What are the key components of the factory of the future?
Trends and challenges in industrial manufacturing and production
Digitalization and technology will heavily accelerate by 2030. However, according to the World Economic Forum (WEF), over 70% of the global production sector is still languishing in pilot phases for the Industrial Internet of Things (IIoT). As a consequence, only very few companies have effectively deployed advanced digital and sustainable production at scale.The potential to untap is still vast. Simultaneously, we see digital solutions and services becoming increasingly ready-to-scale, unleashing tangible benefits of digitalization for shopfloors and manufacturing environments in all industries.
In fact, establishing a factory that is at the same time green, lean, and digital will enable companies to outperform competition in both profitability and sustainability. On the other hand, there are several key challenges to address when kick starting your factory digitalization journey.
In manufacturing, as in any other business, potential transformations will continue to take place in a VUCA (volatility, uncertainty, complexity, ambiguity) environment, which becomes even more visible in today’s turbulent times. Manufacturers will need to operate in a world that is rapidly changing. Events will become less predictable and therefore less reliable for planning. The world’s complexity and ambiguity mean risking poor decision making based on ambiguous information, especially when failing to look beyond the horizon of one’s own operations and integrating the entire ecosystem in decision making. Despite this, if one thing is certain, it's uncertainty, and it is here to stay. We just have to find a way to cope with it.
There is also a certain probability of getting lost in digitalization – a commonly observed pitfall. Companies tend to rush into the idea of implementing IIoT solutions at high speed. However, in most sectors, executives often lack the knowledge to select, adopt and scale the right technologies that could be most beneficial for the company. They tend to become infatuated with a technology without considering the impact and benefit for their business. Worst case scenario, this technology doesn’t fulfill its purpose. Furthermore, most plans and roadmaps lack prioritization, also resulting from a lack of knowledge in digitalization and automation. In short, we see plenty of organizations missing consistent knowledge to elaborate, prioritize and evaluate the benefits of factory digitalization. These organizations will always under- or overestimate the potential impact of these solutions when scaling-up. Without understanding the business value, companies might become entangled in proof of concepts and pilot phases that will never scale sufficiently. The more complex the digital environment gets, the more crucial it becomes to keep a compass with clear direction to avoid getting lost in the digitalization jungle.
In addition, there is another major challenge that shares the spotlight. An ageing population and society means that the labor market will dwindle mid-and-long-term, especially in Europe and the Americas, but also already in some Asian countries. This demographic shift will decrease the available workforces significantly. Therefore, existing staff members must be encouraged and supported by automation and digitalization to facilitate their operations and productivity for a longer period. There is also a need to relieve the shopfloor operator from physical exertion e.g., by handling robotics and automation in conveyor technology, while nourishing their intelligence and creativity supported by digital solutions e.g., through worker guidance or quality assurance. Digital transformation will not work without the right people, so keeping and training them is of highest priority.
Fourth and finally, executives must determine how to implement stricter emissions regulations to achieve sustainability targets for their supply chain and manufacturing processes. ‘Carbon neutral’ is mostly, while still perplexing, measured and realized for the process. In Europe, manufacturers are beginning to tinker with the concept of BAT (best available techniques) to limit emissions from manufacturing. As defined by the OECD; “[…] ‘best available techniques’ means the most effective and advanced stage in the development of activities […] to reduce emissions and the impact on the environment.” However, utilizing data to accurately determine the carbon footprint is highly challenging, especially as supply chains become increasingly complex.
Nevertheless, vertically and horizontally increasing connectivity within entire supply chains allows, based on common digital solutions and platforms, to create this transparency to identify the levers needed to continuously monitor, balance and reduce the carbon footprint.
North stars for the factory of the future
Addressing those challenges takes more than just a plug-and-play solution or deploying applications from an App Store in the systems and assets. The digital transformation in factories comes with a package of unique requirements and ongoing disruptions, which must be opened and addressed to reach the Factory of the Future vision. We need to realize that transformation applies to more than just the factory line or floor. Digital transformation encompasses the whole of your organization, comprising your processes and technology, with people being the stars of the show.
Before transforming your company, you need to identify your north stars. In manufacturing, there are three specific goals to shoot for to create the Factory of the Future.
Productivity is the most obvious one, and it has been there from the start. Even without digitally transforming the factory, a yearly increase of 10 percent is optimistic for many manufacturers. Without a doubt, this increase in productivity is the bottom line to creating lasting commercial success and ensuring competitiveness. These productivity boosts can already be achieved by applying classical lean processes and administration as well as connectivity and automation.
Achieving flexibility is another important destination for digital transformations. The factory of the future will need to meet market uncertainties head-on. Variations in demand, smaller lot sizes and increased uncertainty in complex supply chains will have to be tackled while avoiding, or even better, cutting waste in factory processes. Automation and cutting-edge technologies like IoT and AI, as well as the transparency achieved through their implementation, can help executives reach that flexibility destination.
Sustainability is not only critical for meeting BAT-compliant production models, but methods in manufacturing that support sustainability goals, achieved with digital transformations, are crucial for combatting climate change. Additionally, public opinion on climate change is shifting towards a demand for more sustainability. As a result, signaling the achievement of your sustainability and decarbonization goals, through digital transformation and energy efficiency, will also improve your corporate image.
Before transforming your company, you need to identify your north stars. In manufacturing, there are three specific goals to shoot for to create the Factory of the Future: productivity, flexibility and sustainability.
How to strive towards the factory of the future?
To create a sufficient backbone for the digital factory of the future, you need to foster changes in the areas of processes and organization, people and culture as well as scaling technologies. It is crucial to understand that digital transformation affects every aspect of an organization.
Adapting processes and organizational setup to lean principles
Peeking into one our client’s sites, cost pressures demand that companies streamline operations and add more digitalization to achieve higher efficiency in manufacturing processes. Siemens’ Lean Digital Factory approach offered the necessary transparency to demonstrate to our client how to successfully use digitalization in a discrete industrial manufacturing environment. What we often still see are missing interfaces for horizontal and vertical integration, overcomplex processes and systems, and many uncoordinated or even competing initiatives that over work the staff, resulting in a chaotic working atmosphere.
Companies have always been aiming for process improvements that lower costs and time-to-market. By doing so, efficient, waste-free processes are (still) the way to go to maximize the value that modern technology offers. Digital technology can be applied to all processes in production, logistic, administrative processes, and even the organizational structure. The organizational structure itself helps to efficiently organize people’s responsibilities and communication channels throughout the process.
In the factory of the future, processes are designed to be simple, built on direct communication and fewer interfaces. Building and adapting processes with a lean and digital mindset means avoiding uncertainty and unclear responsibilities. Processes and organization need to be programmed to consider the opportunities and limits of digitalization, e.g., for communication and general information flow. As a result, you can develop touchless processes that are built on data-driven decisions.
In the end, digitalization will enable progress, and it will foster innovation by giving transparency on current processes and scenarios and making data-driven decisions based on these insights. This approach will boost your productivity to new dimensions to reach your sustainability and flexibility goals.
Enabling people’s digital mindset and a learning culture
The pursuit of technological progress, efficiency and sustainability can foster a culture of continuous development, but siloed knowledge, that has traditionally rested with experienced and qualified individuals, will need to be extracted and shared company-wide. It needs to become institutional knowledge.
Broadly speaking, what needs to be fostered is an environment in which employees appreciate your company’s vision and translate it into action. There needs to be a shared vision in place to achieve the common goals across your enterprise. As a result, your digital factory can be a place where employees see a particular problem as an opportunity to improve the entire enterprise. You need to make your people part of the digital solution from the get go.
To successfully progress in digitalization, your organization needs to motivate and engage employees to build a culture with digital elements. Initiating the change to an employee digital mindset will coincide with raising curiosity of the new digital work environment. This can range from building expert communities, that work together across organizations and hierarchies, to re-thinking your collaboration in interactive online events and workplace planning.
This change requires constant training and aiming towards attaining and building the right mix of competences. In order to do this, you need to identify your individual skills gap and areas for improvement. In many cases, this means re-thinking job profiles and offering individual learning opportunities. You must also make sure to foster digital learning and give employees the stage to share their knowledge. Mentoring and coaching can be a great addition to the set methods of learning from within and from outside your organization. Remember, people make digital transformations happen while technologies are only the tools needed to get there.
Scaling and combining Industry 4.0 and green technologies with IoT
Technological advancements have been the main driver of past industrial revolutions and are still essential for industry 4.0 development. Modern technologies such as cloud computing, machine learning and the industrial internet of things (IIOT) create a connected organizational environment that allows constant exchange and analysis of data between systems and physical assets.
To ensure a consistency of successful implementation, project companies require scalable and proven solutions that build on interfaces and scalable design. This is facilitated by using reference architectures and choosing from existing best practice solutions from an established solution library. To achieve net zero, this library should also include solutions that serve the main purpose of neutralizing the carbon footprint.
The crux lies in the successful implementation of these digital solutions. You need to make sure your strategy allows you to collect accurate and continuous data, and this is only realistic when building on blueprints and design principles for infrastructure and leveraging scalable solutions.
Connecting the worlds of information technology (IT) and operations technology (OT) will do the trick to build the factory of the future. While these areas did not particularly overlap in the past, the full integration of IT and OT will create unique insights generated from plant and operations data. With data-enabled technology platforms, the organization can gain transparency and smooth access to existing and planned digital solutions. In the end, choosing the right green and digital solutions, connecting them based on existing blueprints, and making them scalable will be the success factors for your factory of the future. The technology to tackle the climate crisis is here – we just need to leverage it correctly.
By doing so, cloud-based networks, AI, and automation will cause more disruption in the next five years than anything we’ve seen before, like in the Automotive sector.
Conclusion
The factory of the future will realize its full potential for sustainability, productivity, and flexibility by transforming not only processes but people, organization and technologies. Scalable digital solutions will play a key role in this transformation. Only with a holistic factory digitalization approach in the palm of your hands will your factories be able to address the challenges of tomorrow.
Digital solutions will also be our only hope when trying to tackle the climate crisis. Producing goods in the most resource efficient and sustainable way will only be possible if you have the data prepared and analyzed to make the right decisions. Remember, there is no sustainable transformation without a digital one.
Siemens Digital Industries has launched an ongoing program that has been in place for four years. Involving over 30 plants, Siemens has taken more than 800 measures in five key areas resulting in an 8% increase in productivity. The program is currently scaled up to incorporate more factories, regions, and businesses. This way, Siemens will reach its ambitious goal of staying competitive in the market and paving the way for its sustainable and carbon neutral future: Green, Lean and Digital – the Factory of the Future!
Free whitepaper
Based on our unique experience in digital factory environments, we identified several company as well as use case specific factors to make the groundbreaking decision between edge and cloud. Download our whitepaper and learn which factors to consider when unlocking the full potential of your IIoT journey!
Our expert
Author
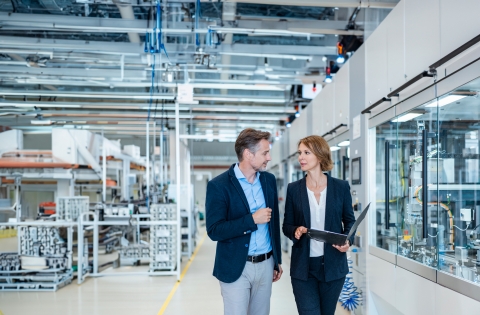
Digitalization with Purpose
Digitalization with Purpose – Uncovering Data to Create Utility Stakeholder Value
All data is not equal and data access alone will not deliver value to your enterprise.
For a simple statement, it is one that carries significant consequences. For every bit and byte of data exchanged from central, enterprise platforms to edge and connected devices or assets, there is a specific cost and value to the business and its stakeholders.
At a unit level the TOTEX (total expenditure, including upfront capital outlay and ongoing operational costs) associated with each byte of data may be small; however, with the exponential growth of data, related costs will continue to rise.
While that rise may not be as steep as the growth in data volume overall, the continuing fall in the cost of data storage is flattening out, meaning businesses need to look more closely at how they manage their data to keep costs under control.
The accumulation of data in isolation does not yield outcomes or deliver business returns. Data must be consolidated and consumed to turn it into value.
Data offers new opportunity
So how should data be viewed strategically, if not as a direct source of value but one with an inherent cost? Ultimately, data is an enabler – it enables use cases and applications, which solve the business challenges of today and support the ongoing advancement of an organisation for its stakeholders.
The potential value of data is equally reflected within the art of the possible – the emerging topics and innovative ideas that are yet to be conceptualised by the best and brightest of our global society yet to be brought to market which will increasingly rely on data to disrupt and progress.
Clearly data and information provide a basis to construct value and insight, which would be inaccessible without it. The emerging data-driven solutions of today and tomorrow will be a key facet within the necessary evolution and transformation of our utilities, cities and societies, as part of a net carbon zero future.
However, Rome was not built in a day and digitalisation represents more of a journey than a destination. It is vital, therefore, that we acknowledge that there is no silver bullet when it comes to digital and data enablement.
Challenges will be witnessed throughout the journey of individual organisations, evolving based on the maturity and capability of the existing systems, strategy and personnel at their disposal.
Understanding digitalisation challenges for utilities
As we uncovered during my last blog, global spend within the Industrial Internet of Things (IIOT) is rising. In 2020 it was valued at USD 216.13bn, 20% of which is directly attributable to the energy sector. Investment at this scale will create transitional risks for utilities, but these can be mitigated with a prudent approach to business digitalisation strategy, planning, implementation and management.
As data volumes grow throughout the energy sector, there will be an unequivocal need to provide robust cyber security, auditability, standards adherence etc, and to control processes for stakeholder access to data. With individual platforms and systems, this can be challenging enough; when considering the wider direction of enterprise IT/OT integration, these headaches will be compounded.
A greater focus upon platform and system integration will increase the pressures on legacy systems to scale and meaningfully participate within an increasingly open digital environment. It is not too far-fetched, therefore, to suggest that there will be a push from both internal stakeholders and external suppliers to procure new, digitally native, application rich products and systems which can critically scale.
This increases the risk of stranded assets throughout the enterprise estate, both today and tomorrow. For example, how confident are businesses that software and products procured today will scale and grow with your organisation, aligned to your respective digitalisation strategy, throughout the mid-to-long term?
The sunk cost of data
Stepping away from technology, challenges also emerge when considering the sunk cost of data and its management, not just in storage and communications, as noted previously, but also in terms of the digital fluency of a workforce.
Tellingly, 47.3% of European transmission and distribution operators questioned in IDC's 'Utilities Core Business Transformation Survey 2021' confirmed that a lack of digital skills amongst employees was the largest internal challenge when investing in new technology. In comparison, the second highest challenge was budget and financial constraints, capturing 29.7% of the respondents’ concerns.
Then consider the challenge associated with determining the business impact of these investments. How frequently is Return on Investment (ROI) calculated and evaluated within digital procurement? How is this tracked throughout the operational lifecycle of the system?
Furthermore, how are the associated Environmental, Social and Governance (ESG) benefits monitored? These are aspects that are becoming increasingly important within the push for meaningful change in terms of reduced in carbon consumption over the coming decade. If businesses are unable to accurately document determine these required outcomes and benefits ahead of procurement up front, it is highly likely such KPIs will not be monitored nor realised during the lifecycle of the solution.
These points contextualise some of the typical challenges faced by utilities as part of digital transformation programmes. It is increasingly clear that the success of digitalisation initiatives depends on the provision of a client-orientated solution and outcomes, rather than potentially siloed digital products and offerings.
Avoiding pitfalls – how can digitalisation be de-risked?
Regardless of macro similarities, no two utilities are the same. Each business requires results consistent with its strategic direction, encompassing the underlying enterprise estate.
A client-driven solution goes some way to addressing nascent risk, though equally important is that solutions are underpinned with best-in-class common values – an effective set of guiding principles. Guiding principles offer consistency in approach, incorporating decades of best practice to minimise inherent risk within complex delivery.
Focus on business impact and ROI – All things data and digitalisation have inherent cost but this need not be a barrier to progression. The supporting business case for each investment should demonstrate where and how value can be created throughout the organisation.
Transparency in terms of target ROI and ESG benefits is critical because these elements provide justification as part of a robust business and investment case. Documenting how a utility company will benefit against its individual operational and strategic KPIs is a must.
Maximising the use of existing client investments – Throughout the operational lifecycle of any system there will be the need to maintain and even extend or enhance – activities which bear consequential cost. Driven by client need, building around and upon existing core systems to focus efforts within the enterprise IT estate can maximise existing capabilities and skills throughout the business, whilst limiting investment in new technologies.
If, for example, core systems can be enhanced to sanitise valuable data for wider use, this is likely to reduce investment cost in the enabling efforts and associated spend, thus improving ROI when creating new data-driven value.
Target Minimum Viable Data (MVD) – If not all data is equal, the task of prioritising which data offers most utilisation potential and consistency to support impactful use cases and applications is a vital activity. Determining what data exists, and what is accessible, creates a bespoke data landscape for your business – the MVD baseline.
Grow with your data landscape – As digitalisation is a journey rather than a destination, generating the MVD baseline to rapidly enable value with accessible data is critical. As your business and its ecosystem of increasingly connected technologies and digital personnel develop, so can the MVD baseline itself.
Therefore, providing a mechanism through open and scalable APIs for example, to integrate additional data from existing or emerging sources is essential to enrich and unlock additional digital value.
Coordinate data and increase accessibility – In collating a reusable MVD baseline, the opportunities to increase transparency and structurally open access to internal business stakeholders (subject to relevant access and governance requirements) becomes increasingly compelling.
How could the business benefit with an increasingly transparent approach to inter-departmental data access? What business challenges could be solved in new and innovative ways? In post-COVID operations, could data access and transparency support social cohesion for remote staff and increase digital fluency of the workforce?
The recent Gartner CDO Survey suggests it could. According to the survey, data and analytics leaders who increased data sharing led teams that were 1.7 times more effective at showing demonstrable, verifiable value to stakeholders.
Get your people on board – Early buy-in from employees, from the conceptualisation to implementation stages, helps to mitigate the scepticism often felt within a business in times of change. As presented within this Siemens Advanta blog, it is important to consider that digital transformation can often be as much a cultural transformation as it is a technical one.
Early engagement of your staff in the journey itself will help determine native digital fluency throughout the business, supporting the identification of internal experts, plus those areas that require future training and development.
These principles are constructed upon time-proven best practice and decades of solution implementation experience, underpinned by common sense. They are designed to directly reduce the risk and effort associated with data-led value enablement.
Embedding these principles supports the goals of early identification of business value based on common and existing data, and minimising enablement cost and business disruption in terms of systems and personnel alike. Consequently, these principles can be directly mapped within a wider strategic digital transformation approach, known as the ‘Digital Core’.
What is digital core?
Digital Core is a term occasionally used in the industry to describe technology platforms and applications that support business transformation, enabling organisations to address the needs of nascent and evolving markets considered within the digital economy.
Central to our Digital Core thesis is the consideration that existing and legacy systems cannot and will not be replaced overnight. Certainly, there will be times when operational systems reach the end of their working life, fail to integrate or even scale, at which point strategic product replacement will lead the way.
However, it is reasonable to assume that the constellation of operational systems in place throughout today’s modern utility landscape is likely to broadly reflect the enterprise environment in operation towards the end of the decade.
Therefore, to our team at Siemens Advanta, the Digital Core represents a mindset and approach, as much as technology and solution.
The Digital Core enables facilitates transformation; its adoption enables businesses and their stakeholders to build upon existing investments and extract data from operational core systems with focussed investment, to create new business value, underpinned with a clear business rationale. This, in essence, is harnessing the data that is being created and stored today throughout your organisation.
Digital core: systematic engagement and analysis
From a methodology and engagement standpoint, the Digital Core requires a baseline of technologies and systems which are strategically relevant over the mid-to-long term for a client. The theory is that each will represent the anchor for digitalisation initiatives over the coming years.
We consider the data from these core systems to be of principle value, as it is likely to be increasingly consistent and even enhanced, throughout a given time horizon, thus worthy of accessing for repetitive re-use.
Analysis of these core systems enables the creation of the MVD baseline, an activity that identifies what data and information exists and documents what is subsequently accessible today from these core systems. This environmental analysis of strategically and operationally relevant systems documents the data landscape and digital maturity of each core system.
Additionally, robust engagement sets out to understand and document the challenges faced by clients. In discussing business pain points and framing strategic and operational hurdles, it is feasible to derive data-driven resolutions in the form of new use cases and applications. Each of these can be subjected to cost-benefit analysis to calculate independent ROI.
Furthermore, this analysis includes consideration of the typical input data expected to bring individual use cases to fruition, tying the value directly back to the enabling, underlying data itself.
A gap analysis follows, assessing generated/accessible data from the business against highlighted use cases and input data. Any significant gaps can be either addressed via business change management to trigger additional data discovery or, where relevant, with targeted access to third party data, such as Metrological data. Armed with this insight, use cases could be reprioritised based on the MVD baseline and cost to supplement or extend. The outcome of this consultative process is to derive a common MVD landscape, which encompasses the following elements:
- MVD baseline – an overview of the data generated within the business from identified key systems, acknowledging which is and is not accessible to the business.
- Business challenges and resolutions – highlighting defined use cases alongside the common data required to enable each.
- Data gap analysis – available data versus use case comparison.
- ROI review – framing cost-benefit of key use cases from existing business data
As a consolidated activity, this gives a robust insight into the digital environment of any client, documenting how current data can address key challenges and create new value when enabled via the digital core.
Digital core: a client-driven solution
The Digital Core is not only a consulting activity but also the provision of a client-orientated solution. Tasked to access the MVD baseline from core business systems, it facilitates the creation of impactful use cases via a reusable and accessible integrated solution.
In creating a common, reusable and accessible data framework or MVD baseline, the intention is to enable client stakeholders to rapidly ideate, test and develop parallel data-led innovations. At every step of the Siemens Advanta Digital Core journey, value is created, either in analysis and understanding or with rapid prototyping and testing of ideas based on common data.
Depending on the respective requirements of each business, the form of the digital core solution will change. This is to balance the need for on-premise versus cloud technologies and for creating a single source of truth, like the master data of the business data versus a reflective data extract from core systems.
Once available, this promotes wider internal access to useful data, away from critical business systems, with governance factored into the solution. Thus, the need to really understand what data you have, where it came from, where it goes, security implications and its quality is satisfied. Such technical considerations will be explored further in a later blog.
As the digitalisation journey progresses, the MVD baseline can be extended with additional, richer data and information, compounding the enabling value of data held within the digital core.
In some regions, such as the UK, there is even a push towards ‘presumed open data' from the energy sector. This involves requiring that utilities, amongst others, reveal data to external parties, with the ambition to foster whole systems thinking and innovation to address sustainability and energy-related challenges.
The digital core methodology and solution accommodates even such a progressive take on data sharing, whilst providing governance and internal value creation simultaneously.
Delivering value from digitalisation should not be held to ransom over big data aspirations. Using a common or emerging MVD baseline to demonstrate quick wins in the form of a Proof of Value and Minimum Viable Products will promote longevity and acceptance of the broader digital transformation initiative.
Streamlining investment to deliver greater returns
According to a Siemens Advanta HBR pulse survey, 80-90% of respondents can’t or don’t accurately measure ROI for digitalisation initiatives. Given this, it is somewhat unsurprising that between 60% and 85% of digital transformation initiatives have failed. You can find more detail in our white paper, Internet of Things: From Buzzword to Business Case.
The paper spells out the direct costs associated with IoT/digitalisation initiatives, including applications, platform/solution, communications and devices/assets. It also quantifies the transition costs that align to the business and its adoption of new technologies.
Transition costs include the processes and tools, skills and personnel development that go alongside change management – all critical factors when considering the true cost of digitalisation.
A realistic ROI assessment will not yield a singular outcome. However, when considering variable uncertainty ranges within the calculation, the credibility of the results increases dramatically, as shown in the white paper.
The ROI analysis can, therefore, be enhanced when adopting a specific lens towards global utilities, offsetting the direct and transition costs against benefit created for the business.
As part of an activity called ‘360 business impact reflection’, analysis considers how data access and new use cases will impact the business. It addresses individual or shared challenges throughout internal departments with, for example, cost savings, efficiency benefits and improved KPI adherence.
This task includes the effort to prioritise and analyse common KPIs consistent with many utilities worldwide, based on the respective organisations. Examples include:
- Planned network interruptions
- Unplanned minutes lost
- Number of faults
- Inspection and maintenance cost
- Network reinforcement and refurbishment
- Asset health
- Customer satisfaction and complaints
- Cost to serve
- Time to connect
- Environmental management
These KPIs align within broad strategic pillars for utilities, which commonly include:
- Delivering a safe and reliable network
- Improving environmental impact
- Improving network connections
- Enhancing customer satisfaction
- Supporting vulnerable customers
360 business impact reflection in action
To explore the concept of 360 business impact further, let us take a specific example: heightened vulnerability of network assets due to sub-optimal network planning. In this example we’ll consider three key departments of the utility: 1) network planning, 2) network operations and 3) customer services.
- Suboptimal network planning can intrinsically increase the risk profile of the asset fleet throughout the network. 360 business impact reflection considers the effectiveness of asset intervention programmes, how asset risk is determined and the replacement/upgrade of each asset managed.
- The outcomes of this shortfall roll into network operations. Higher asset risk is likely to increase the number of faults and related costs of the network, potentially decreasing the operational lifetime of fleet assets and in turn increasing asset replacement cost.
- With increased faults come increased outages, impacting the customer in terms of minutes lost and supply interruptions. These factors are likely to come back to the customer services department, which must respond to stakeholders, both customers and regulators, as to the network performance.
- Such topics can additionally be reflected in the time to quote and connect of the connections department.
(Digital Core) Process + Solution = Outcomes
The cause and effect of decisions and activities is a constant within any operational environment and, as noted previously, digitalisation is not a silver bullet. However, what can be provided is richer, more powerful insight, using data from existing systems, manifested within new use cases, to solve current and future business challenges. As an inclusive and accommodating methodology, understanding the specific circumstances of each client, the Siemens Advanta Digital Core ensures a financially appropriate outcome is realised with clear investment rationale.
By linking the enabling and value creation activities, built upon existing client systems, and addressing specific business challenges using current and available data, it drives and unlocks impactful use cases as part of a tailored solution for your business.
Free whitepaper
Discover the Internet of Things and the challenges that need to be solved in a digital transformation. Get insights how to create value when optimizing processes or generating new business models out of data.
Our expert
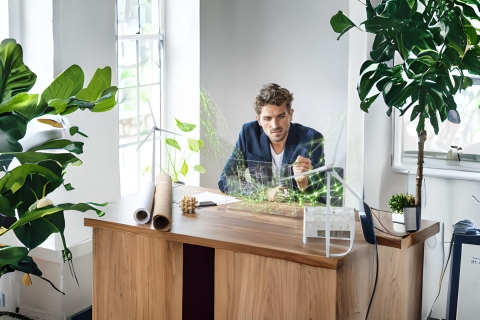
Pagination
- Previous page
- Page 3
- Next page