Navigate the Impact of Tariffs on your Supply Chain
Navigate the Impact of Tariffs on your Supply Chain
Tariffs and global supply chains are more interconnected than ever. Organizations face heightened risks, rising costs, and operational complexity as trade tensions and regulatory shifts continue – especially following US-China tariffs and retaliatory measures.
How tariffs affect supply chains – and how to stay resilient
The impact of tariffs extends far beyond added import duties. They influence sourcing strategies, supplier relationships, production timelines, logistics networks, and customer pricing models.
To manage these dynamics effectively, Siemens Advanta’s Supply Chain Tariffs Analytics Solution helps organizations to:
- Model real-time scenarios to assess the impact of tariffs on logistics, costs, and supply continuity
- Analyze root causes at part level to identify vulnerabilities and evaluate dual sourcing opportunities
- Shift perspectives between revenue and spend to better engage customers and suppliers with actionable insights
From disruption to strategy: leveraging supply chain shifts as opportunity
Tariff-related disruptions are no longer isolated events – they’ve become a recurring feature of global trade. To remain competitive, organizations must respond quickly and strategically to changing trade policies and supply chain impacts. This requires a shift from reactive mitigation to active opportunity management.
Turning disruption into advantage means understanding where volatility can open doors: for example, by optimizing production footprints, securing more flexible sourcing models, or rethinking logistics strategies with a long-term view.
How Siemens Advanta helps you build resilience and agility
To support organizations in navigating these challenges, Siemens Advanta provides tailored solutions across multiple dimensions of supply chain strategy. Siemens Advanta supports your organization through:
- Supply chain optimization: improve efficiency by up to 30% and reduce lead times by 40% through nearshoring, real-time tracking, and automation.
- Market diversification: leverage tariff engineering and supplier shifts to reduce expenses by 10–25%.
- Innovation and cost reduction: boost productivity by up to 50% and lower compliance costs with AI-powered analytics.
- Strategic partnerships: recover up to 99% of duties paid via duty drawback programs and free trade zones.
Strategic tariff mitigation: more than cost savings
Mitigating the effects of tariffs isn't just about protecting margins—it's about building long-term resilience. Siemens Advanta’s approach combines technology, analytics, and industry expertise to:
- Identify cost-saving alternatives
- Collaborate with key suppliers using proprietary cost insights
- Support make-buy decisions and product redesign evaluations
Stay ahead of tariff impacts on your supply chain
In a volatile global trade environment, proactive planning is critical. Siemens Advanta’s innovative solution enables businesses to mitigate risks, enhance supply chain resilience, and drive sustainable growth.
Contact us today to learn how we can help you adapt to supply chain tariffs and thrive in the face of uncertainty.
Industry Experts
Accelerating the Future: Strategic Pathways for Emerging Battery Cell Manufacturers
Accelerating the Future: Strategic Pathways for Emerging Battery Cell Manufacturers
Emerging manufacturers face immense pressure from EV makers, investors, and fierce competition amidst market volatility. The rapidly growing battery cell market demands speed and scalability. Those who can quickly ramp up gigafactories will lead the future of energy and transportation.
Speed and Scale – High Pressure on Emerging Battery Cell Manufacturers
The battery cell market is gaining significant traction, presenting a booming opportunity for emerging manufacturers. To capitalize on this growth, these manufacturers must prioritize innovation and speed while navigating a complex landscape to dominate the rapidly evolving electric vehicle (EV) market in the long-term. They face numerous challenges: EV makers demand swift, reliable supply chains and high-performance batteries, investors seek rapid returns and high multipliers, and there is fierce competition from established players with advanced technologies and large-scale production capabilities. Market volatility further complicates the scene, with EV demand projections for 2024 falling short, creating uncertainty through 2030. In this high-stakes environment, the ramp-up of gigafactories is crucial, as the ability to scale quickly has become a decisive factor for new manufacturers determined to lead the future of energy and transportation.
Why Speed is King – Addressing Triangular Pressures in a Volatile Market
The global EV market, valued at USD 388.1 billion in 2023, is projected to reach USD 951.9 billion by 2030 with a CAGR of 13.7%. Despite this, current delays in meeting the 2024 forecast create a volatile market. S&P Global reports that the anticipated EV demand boom for 2024 hasn't materialized, resulting in uncertain projections for 2030 growth. With global EV sales projected to grow by 36% in 2024, down from 62% in 2023, battery cell manufacturers face pressure to adapt. Economic challenges, including high interest rates in Europe and the US and a saturated Chinese market, contribute to this slowdown. Manufacturers must navigate tensions between EV makers, investors, government requirements, and industry players, showcasing their adaptability in a rapidly changing market.
1. Pressure from EV Manufacturers
EV manufacturers stress the need for quick, reliable supply chains, often setting strict deadlines for battery cell providers. Contracts typically include rigorous schedules, with delays leading to financial penalties and reputational damage. The demand for high-energy-density, fast-charging batteries in short development cycles adds additional pressure. Manufacturers must produce lighter batteries with shorter charging times, extended ranges, and reduced carbon footprints, all while meeting high-quality standards. The push for efficiency and excellence in production and quality underscores the intense demands on the EV supply chain.
2. Investor and Government Expectations
Battery cell manufacturers also face significant pressure from investors and competition for government support. Investors expect rapid production scaling within 3-5 years, demanding quick gains and substantial profits. This forces manufacturers to prioritize speed, efficiency, and cost-effectiveness. The need for considerable funding to scale up adds further pressure, requiring strong growth potential and adherence to demanding schedules. Competition for government incentives like tax breaks, grants, and subsidies is fierce. Emerging manufacturers must swiftly adapt strategies to meet eligibility criteria and align with investor and government demands to secure support.
3. Competition from Established Players
Leading companies dominate the battery cell manufacturing market with efficient, large-scale production facilities, setting high capacity and efficiency benchmarks. They use advanced techniques and innovative technology to produce high-quality batteries at lower costs, creating a cost-competitive advantage. This pressures other manufacturers to scale up rapidly while keeping costs low. To stay competitive, new battery cell manufacturers must streamline and accelerate their production processes to reduce costs without compromising quality.
Considering the triangular pressure, the role of gigafactories becomes critical in addressing the industry's demands for speed and scale. These production facilities are designed to meet the high-volume needs of the EV market, promising swift and efficient battery cell manufacturing to keep up with the fast-paced growth and innovation. Gigafactories, with their capability to ramp up production quickly, offer a strategic solution for emerging manufacturers to tackle the pressures of rapid scaling and market volatility.
Gigafactory Hurdles – Fast Ramp-Up and Scaling Challenges
Building a gigafactory and scaling up production involves overcoming intricate challenges. Emerging battery cell manufacturers must adeptly navigate each stage to achieve large-scale sustainable manufacturing.
1. Strategy & Setup
The success of a gigafactory depends on thorough strategic planning and meticulous operations setup. Analyzing target customer adoption rates and battery cell demand is crucial to accurately predicting market demand. This ensures that the factory's strategy aligns with future needs. Securing adequate funding is equally important, as large-scale projects and expansions require significant financial resources to support construction and operations.
2. Product Design
Emerging battery cell manufacturers must balance advanced materials and innovative designs with cost constraints. This requires continuous innovation to maintain economic viability while optimizing energy density and thermal management to maximize storage capacity and minimize size and weight. These efforts align with Design for X (DfX) principles, emphasizing manufacturability, cost-efficiency, and sustainability. Ensuring cell safety and stability prevents risks such as overheating or short circuits. Additionally, achieving consistent performance over numerous charge and discharge cycles is vital for longevity.
3. Factory Design & Planning
Securing an optimal location requires a balance between proximity to raw materials, market access, and logistical efficiency. Access to green energy sources is increasingly important to enhance the sustainability of the batteries. This directly impacts the facility's operational efficiency and cost-effectiveness by reducing transportation costs, ensuring reliable supply chains, and lowering energy expenses. Additionally, creating a scalable and adaptable layout is crucial for responding flexibly to market changes and accommodating future technological advancements and shifts in demand, ensuring the facility remains competitive and efficient.
4. Build, Commission & Ramp-Up
The build, commission, and ramp-up phase involves several critical tasks. Integrating and stabilizing new equipment requires meticulous oversight and collaboration with machine builders to ensure efficient manufacturing processes and prevent delays and cost overruns. Hiring and training a skilled workforce is equally important, as advanced manufacturing processes demand highly qualified employees to manage sophisticated systems and ensure smooth operations.
5. Operate
Once operational, a gigafactory must manage ongoing complexities. Handling maturing processes is a significant task, with errors occurring from electrode production to module packing, often making stacking a bottleneck process that requires continuous improvement and careful monitoring. Scaling up production while ensuring process stability is crucial. As the gigafactory footprint expands, maintaining stable processes in new environments, such as additional production lines or new facilities, is essential to uphold product quality and operational efficiency.
Holistic Planning – Leveraging Automation and Digitalization for Rapid Scaling
Emerging battery cell manufacturers must take a holistic approach, integrating advanced planning, automation, and digitalization to overcome these challenges and ensure rapid scaling.
Advanced Planning
Advanced planning forms the foundation for successfully ramping-up and scaling a gigafactory. This involves several critical components:
- Integrated Market Analysis and Forecasting: Accurately predicting market demand and trends is vital. Manufacturers can accurately forecast EV adoption rates and battery cell demand using advanced analytics and predictive modeling. This ensures strategic alignment with market dynamics, reducing the risk of over- or undercapacities.
- Strategic Financial Planning: Securing sufficient funding and financial backing is essential for large-scale projects. Understanding the major cost drivers of a battery gigafactory enables better decision-making and reduces CAPEX and OPEX. Developing robust financial models, engaging with a diverse range of investors, and establishing clear financial goals and milestones ensures the availability of necessary financial resources.
- Digital Twin Technology: Enhancing gigafactory design and planning with digital twin technology allows manufacturers to create virtual models of the gigafactory. This enables detailed simulation and optimization of production processes, facilitating flexible and scalable factory designs. Additionally, virtual equipment commissioning accelerates new product introduction in a "safe" environment.
- Virtual Product Design: Balancing performance and cost through virtual product design is essential. Engineers can analyze thermal management, electrochemical performance, and mechanical stresses under various conditions by simulating physical behavior and rapidly validating designs. This approach identifies potential issues and optimizes designs before building physical prototypes, saving time and resources.
Automation
Automation is an essential component in enhancing production efficiency and scalability within gigafactories. Key aspects include:
- Advanced Manufacturing Systems: Implementing advanced automated production lines, robotics, and AI-driven quality control systems reduces manual labor, minimizes errors, and increases production speed and consistency. Transitioning from predictive to adaptive systems necessitates close collaboration with machine builders to achieve the target operating model.
- Automated Testing and Feedback Loops: Integrating automated testing systems that provide immediate feedback and adjustments to production processes, enhancing overall product quality and reducing waste.
- Energy Management Systems: Integrating automated energy management solutions optimizes energy consumption, reduces costs, and enhances sustainability. Smart grids, AI-based energy forecasting, and automated demand response systems contribute to more efficient energy use within gigafactories.
Digitalization
Digitalization is vital for enhancing operational efficiency and resolving bottlenecks in gigafactories. Key elements include:
- Data-Driven Decision Making: Implementing IoT sensors, real-time analytics, and AI-driven decision support systems at every production stage provides actionable insights for continuous improvement and quick issue resolution. Real-time data collection and analysis help identify inefficiencies, predict maintenance needs, and optimize processes, with AI offering predictive analytics and automated responses.
- Digital Twin of Production: This technology improves operational efficiency by simulating processes and predicting outcomes. The virtual model enables testing and optimization in a digital environment, leveraging real-time data and analytics to foresee issues and suggest improvements. Consequently, it boosts efficiency and reduces downtime.
- End-to-End Digital Integration: Integrating end-to-end digital systems across the supply chain, production, and distribution networks into a single cohesive digital platform enhances coordination, reduces information silos, and improves overall operational transparency.
Leveraging a holistic approach ensures streamlined operations, cost reduction, and a competitive edge in the rapidly evolving battery manufacturing industry. This comprehensive strategy encompasses all aspects necessary to ramp-up and scale a Gigafactory effectively.
Best Practices – Lessons from a European Supercapacitor Leader
A top-tier European supercapacitor cell manufacturer scaled its production capabilities, positioning itself at the industry's forefront through strategic planning, advanced automation, and digitalization. The company predicted EV adoption rates using advanced analytics and market research, aligning production with future needs and avoiding overproduction risks. Diverse financial models attracted investors, ensuring sustainable growth and operational efficiency. Virtual product design balances performance and cost, creating a sustainable supply chain that meets high market standards.
Implementing virtual commissioning and digital twin technology improved production line setup and testing, reducing planning and setup time by 30% and operational costs by 15%. Flexible factory designs enabled rapid market adaptation, ensuring a competitive edge. Additionally, automation, including robotics and AI-driven quality control, lowered scrap rates by 30% and increased production efficiency by 20 p.p. Data-driven predictions have improved logistics, ensuring timely raw material availability and reducing lead times by 25%. Automated training programs and VR simulations effectively prepared the workforce to operate sophisticated machinery. Digitalization has enhanced operational efficiency through IoT sensors, real-time analytics, and AI-driven decision-making, continually improving production processes and doubling cell output.
Meanwhile, end-to-end digital integration enhanced coordination and transparency across the supply chain, using digital twins to optimize operations dynamically. This strategic transformation allowed efficient production scaling, high-quality standards, and cost reduction, securing the manufacturer's position as a European leader in the supercapacitor cell market. Embracing innovation and strategic foresight, the company met market demands and set new industry benchmarks, solidifying its competitive advantage in the rapidly evolving EV landscape.
Seizing the Future – The Imperative Race for Emerging Battery Cell Manufacturers
As demand for electric vehicles surges, emerging battery cell manufacturers are under intense pressure to keep up with rapid growth, high expectations from EV makers, investor demands, and fierce competition from established players. In this volatile and fast-changing environment, the gigafactory stands out as a critical factor in shaping the future of energy and transportation.
To navigate this uncertainty successfully, manufacturers must embrace a holistic strategy integrating advanced planning, automation, and digitalization. Scaling production quickly and efficiently will be crucial as the battery market evolves. How these emerging players address these challenges will determine their success and profoundly impact the global energy transition and the drive toward a sustainable future.
Battery cell manufacturers must take decisive action now. They can maintain a competitive edge in this ever-changing landscape by investing in thorough planning, focusing on automation, and adopting digital technologies. As the future of energy and transportation unfolds, those who can innovate and scale effectively will lead toward a more sustainable and electrified world.
Our contributors
https://www.marketsandmarkets.com/Market-Reports/electric-vehicle-market-209371461.html
https://www.fortunebusinessinsights.com/industry-reports/electric-vehicle-market-101678
https://www.fastmarkets.com/insights/whats-in-store-for-ev-demand-in-2024-and-beyond/
https://ev-volumes.com/news/ev/global-ev-growth-forecast-in-2024-but-challenges-remain/
Author
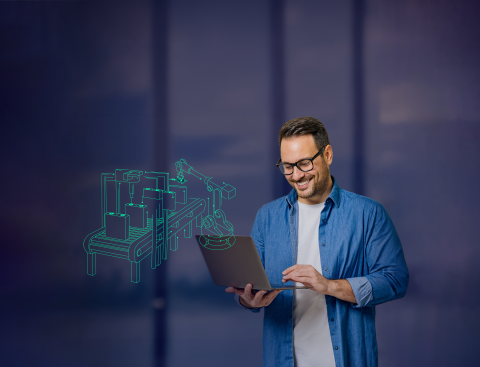
Teamcenter on Azure Assessment Workshop
Teamcenter on Azure Assessment Workshop
Azure offers a plethora of services and features that can supercharge your PLM (Product Lifecycle Management) capabilities. Siemens Advanta´s goal is to facilitate a seamless transition to Azure, Microsoft's cloud computing platform, by identifying the key benefits, assessing potential risks, addressing gaps, and outlining pragmatic approaches for the migration process.
- Scalability: Adapt your resource usage based on current needs without the constraints of physical infrastructure.
- Security and Compliance: Benefit from Azure's robust security features and compliance with industry standards.
- Global Reach: Leverage Microsoft's expansive global network to deploy and manage your applications anywhere.
- Integration: Enjoy seamless integration with a wide range of tools and services available in the Azure ecosystem.
- Innovation: Stay ahead of the curve by utilizing cutting-edge technologies like AI, ML, and IoT to add smart capabilities to your PLM processes
- TeamCenter Audit: Reviewing current systems, processes, and architecture.
- Cloud Readiness Evaluation: Analyzing the suitability and readiness of your current TeamCenter deployment for Azure.
- Cost-Benefit Analysis: Foreseeing financial advantages and implications of the cloud move.
- Security & Compliance Workshop: Navigating data protection, privacy laws, and regulatory requirements.
- Migration Planning Session: Drafting a step-by-step migration plan.
- Identify Benefits: Understand how Azure can enhance specific aspects of your TeamCenter environment.
- Risk Assessment: Address potential security, data sovereignty, and compliance concerns during the transition.
- Gap Analysis: Pinpoint technical and procedural gaps in your current setup that could impact cloud migration.
- Strategize Approaches: Develop a tailored migration strategy, considering aspects like cost-efficiency, minimal downtime, and future scalability.
- Roadmap Creation: Outline a phased plan for migrating and optimizing your TeamCenter environment within Azure
Our industry leaders
Smart Factory Intralogistics
Smart Factory Intralogistics
Operational excellence, automation, and digitalization solutions
Siemens Advanta supports its clients in identifying the digital technologies that can enhance logistic processes in their factories. They provide smart solutions that best fit the logistics processes and help clients identify suitable technologies to change operational processes.
- Performance improvement of you end-to-end intralogistics value chain
- Tool box to drive digital transformation of logistic processes
- Logistics set-up
will be derived from strategy requirements - Right arrangement of intelligent solutions in operations
- Proven impact in our projects
- Reduce your process time by up to -30%
- Reduce your lead time by up to lead time reduction -20%
- Increase your delivery reliability up to +25%
- Help you to optimize your inventory by up to -40%
Our industry leaders
Factory Decarbonization
Factory Decarbonization
Decarbonization & energy efficiency in factories
Siemens Advanta supports its industry clients to leverage sustainability of their factories and factory networks. Our holistic approach enables the journey towards lean, digitalized and energy-efficient factories & production processes by leveraging the entire Siemens sustainability ecosystem covering comprehensive services, scalable (digital) software & solutions and potential hardware applications with a strong implementation focus.
This includes identifying, analyzing, and evaluating energy & carbon emission-related drivers within a factory and its infrastructure, which will create valuable insights for the factory decarbonization journey to reduce energy use, cost, and carbon emissions. Our tailored services and solutions include target setting, data collection, energy assessment, scenario simulation, measure development & roadmap as well as implementation and roll-out.
- Consulting & Integration
- Data Collection & Energy Assessment
- Scenario Simulation
- Optimization Measure Development
- Roadmapping
- Energy use reduction potential
- Energy cost saving potential
- Carbon emission reduction potential
- Optimization measures in roadmap
-
Lean, digitalized and energy-
efficient factory & production processes
Our industry leader
Cost & Value Engineering
Cost & Value Engineering
Providing detailed analysis to identify the optimal approach to source, manufacture and design in innovation and sustainability while reducing cost.
Vendigital as part of the Siemens Advanta organization, drives accelerated cost and value engineering transformation through data.
Cost & value engineering provides another lens, beyond traditional procurement levers, through which to tackle cost challenges. Using a bottom-up approach, we support the process of aligning costs to strategy as well as optimizing the costs of current products and helping to shape future products – ensuring the benefits are maximized across the entire product lifecycle.
-
Value Analysis Value Engineering (VAVE) – assigns a cost to the value or function of a product. By optimizing the relationship between the two, we ensure that products are not over-engineered or under-designed but instead are engineered for the task while keeping costs down.
-
Should cost modelling – we take a bottom-up approach to produce accurate granular level cost calculation for a product or service. These cost models help future procurement cost negotiations, allowing our clients to conduct fact-based negotiations with suppliers.
-
Make versus buy – we help clients understand the true cost of making something in-house versus buying from a supplier. This enables them to make data-backed decisions that support better profitability, stronger business resilience and greater competitive advantage.
-
Design to cost – we support clients to design products with the total cost of design and manufacture in mind. This gives our clients the understanding they need to design a product that is not only fit for purpose but one that can be produced at volume for a profit.
-
Lifecycle costing – accurately profiling the costs of a product over its entire life, from its inception to its decline and end-of-life costs, to understand the total costs involved and successfully forecast and plan for the future.
-
Carbon footprint calculation – we take an in-depth look at the carbon profile of products and their parts to identify those with the highest emissions, before modelling different scenarios and recommending specific actions to help reduce the overall emissions.
- Battery manufacturing assessment – our battery manufacturing assessment helps clients get more transparency around the commercial impact and investment decisions they need to make to ramp up production in battery manufacturing and provides key insights for manufacturing scalability – shaping the art of the possible for tomorrow’s gigafactories.
-
Engineering the product to the right level – we advise on what our clients’ target cost should be for a particular product, component, or the business as a whole. This ensures that a product or component is not over-engineered, therefore reducing spend.
- Enhanced supply chain relationships – we help clients forge better relationships with their suppliers by getting all parties to deal in facts, ensuring transparency and therefore helping reduce cost by getting the right quality of the right part from the right supplier.
- Lower cost and emissions through design - having an accurate data-led cost or carbon calculation allows our clients to make design decisions based on a product’s overall lifetime costs or carbon profile before it enters production.
Our industry leaders
Supply Chain
Supply Chain
Driving supply chain cost reduction while enhancing agility, operational efficiency and resilience against market changes.
Today’s supply chains have become hugely complex, with many moving parts that differ across industry sectors. Taking a data-led approach we work in partnership with clients to build mutually beneficial relationships with their suppliers and implement opportunities to enhance and streamline supply chains while creating greater resilience.
-
Sales & operations planning (S&OP) – we bring together our clients’ sales and operations teams and leverage data from other relevant departments to analyze workflows and projections, optimizing business-wide activity to satisfy demand efficiently.
-
Working capital – we provide the tools and expertise needed for clients to assess their working capital and improve cash flow and ensure a business is in a strong and sustainable financial position.
-
Environmental, Social and Governance (ESG) – a holistic approach that considers the whole supply chain and wider business impact. The aim is to install a sustainable way of thinking and working across the supply chain.
-
Supply chain risk and resilience – helping clients uncover their supply chain vulnerabilities and build flexibility and resilience into their operations to avoid disruption and subsequent loss of profit.
-
Network strategy – implementing the best possible practices and policies for the movement of materials and information throughout the supply chain to achieve optimum efficiency.
- Quality management – implementing industry-specific workflows and technologies to assess product quality and monitor supplier performance while improving consistency and cost-efficiency.
-
Improved efficiency – our in-depth analysis of a client’s supply chain identifies opportunities to improve product, material and information flow creating a more effective supply chain.
-
Reduced risk and increased resilience – we create strategic adjustments to drive performance, mitigate risks and ensure our clients’ supply chains are agile and resilient to any market challenges both today and in the future.
- A more ethical and sustainable supply chain - through data analytics and insight generation we help clients understand their current position against ESG targets, anticipate risks and develop improvements to integrate sustainability into the supply chain.
Our industry leaders
Driving digital transformation and open innovation with a strong ecosystem
Tune in to uncover what the world of open innovation ecosystem holds for the future.
How can cross-collaboration and open ideation help deal with industrial uncertainties? Get your answers from Aymeric Sarrazin and Peter Körte.
Find us also on your favorite Podcast APP:
Apple Podcast, Google Podcast, Siemens.fm,
Stitcher, Spotify (log in to listen on desktop)
Digital Twin & Industrial Metaverse
Digital Twin and Industrial Metaverse
A real-time, immersive Industrial Metaverse connects hardware and software from the edge to the cloud, leveraging the power of AI-enabled, photorealistic, physics-based digital twins to drive efficiency and transform industries, taking industrial automation to a new level. It also changes how we collaborate within organizations, ecosystems, and between firms, their clients, and customers.
We help clients create short and long-term value by combining technology and industry expertise to assess business opportunities, develop transformational strategies, and design, build, and operate metaverse solutions. Our solutions cover marketplace development, blockchain integration, extended reality, digital twins, security protocols, and ecosystems.
- Assessment of business opportunities
- Development of transformational strategies
- Design, build, and operation of metaverse solutions
- Advances in technology can create new opportunities for businesses and enable new forms of communication and collaboration
- Blockchain technology has numerous potential applications that can be optimized through collaborative and immersive virtual environment
- Digital versions have proven to be effective alternatives for marketing, sales, and training
- A digital twin enables virtual modeling of the entire product lifecycle
Our industry leaders
End-of-Life/Recycling-Management
End-of-Life/Recycling-Management
A multitude of external factors, such as increasing commodity prices, stricter regulatory requirements, and material shortages due to geopolitical conflicts (decoupling), turn the sustainable handling of products towards the end of their life cycle into a decisive competitive factor. Derived from practical expertise, our consulting offering helps efficiently secure your supply and market access by closing the circular loop.
- Developing effective and profitable end-of-life programs to support growth and sustainability
- Ensuring long-term access to competitively priced strategic secondary materials
- Creating partnerships and ecosystems to enable circular models
- Leverage R-strategies (e.g., reuse, reman, recycle) to preserve components and materials in a closed loop
- Reduce your carbon footprint through increased use of recycled materials
- Increase resilience of your supply chain through reduced dependency on primary resources
- Grow revenue through new circular business models (e.g., as-a-service, repair, remanufacture)
- Improve brand reputation and customer loyalty through sustainable practices
Our industry leaders
Pagination
- Page 1
- Next page