Navigate the Impact of Tariffs on your Supply Chain
Navigate the Impact of Tariffs on your Supply Chain
Tariffs and global supply chains are more interconnected than ever. Organizations face heightened risks, rising costs, and operational complexity as trade tensions and regulatory shifts continue – especially following US-China tariffs and retaliatory measures.
How tariffs affect supply chains – and how to stay resilient
The impact of tariffs extends far beyond added import duties. They influence sourcing strategies, supplier relationships, production timelines, logistics networks, and customer pricing models.
To manage these dynamics effectively, Siemens Advanta’s Supply Chain Tariffs Analytics Solution helps organizations to:
- Model real-time scenarios to assess the impact of tariffs on logistics, costs, and supply continuity
- Analyze root causes at part level to identify vulnerabilities and evaluate dual sourcing opportunities
- Shift perspectives between revenue and spend to better engage customers and suppliers with actionable insights
From disruption to strategy: leveraging supply chain shifts as opportunity
Tariff-related disruptions are no longer isolated events – they’ve become a recurring feature of global trade. To remain competitive, organizations must respond quickly and strategically to changing trade policies and supply chain impacts. This requires a shift from reactive mitigation to active opportunity management.
Turning disruption into advantage means understanding where volatility can open doors: for example, by optimizing production footprints, securing more flexible sourcing models, or rethinking logistics strategies with a long-term view.
How Siemens Advanta helps you build resilience and agility
To support organizations in navigating these challenges, Siemens Advanta provides tailored solutions across multiple dimensions of supply chain strategy. Siemens Advanta supports your organization through:
- Supply chain optimization: improve efficiency by up to 30% and reduce lead times by 40% through nearshoring, real-time tracking, and automation.
- Market diversification: leverage tariff engineering and supplier shifts to reduce expenses by 10–25%.
- Innovation and cost reduction: boost productivity by up to 50% and lower compliance costs with AI-powered analytics.
- Strategic partnerships: recover up to 99% of duties paid via duty drawback programs and free trade zones.
Strategic tariff mitigation: more than cost savings
Mitigating the effects of tariffs isn't just about protecting margins—it's about building long-term resilience. Siemens Advanta’s approach combines technology, analytics, and industry expertise to:
- Identify cost-saving alternatives
- Collaborate with key suppliers using proprietary cost insights
- Support make-buy decisions and product redesign evaluations
Stay ahead of tariff impacts on your supply chain
In a volatile global trade environment, proactive planning is critical. Siemens Advanta’s innovative solution enables businesses to mitigate risks, enhance supply chain resilience, and drive sustainable growth.
Contact us today to learn how we can help you adapt to supply chain tariffs and thrive in the face of uncertainty.
Industry Experts
Plant Maturity Assessment
Factory Maturity Assessment to increase your operational performance
Enroll in a comprehensive factory maturity assessment by filling out our form. This assessment covers key areas such as manufacturing execution & process automation, supply chain, people & culture, and cybersecurity & operations. Gain transparency on your digitalization potentials and receive a tailored roadmap to enhance your performance.
Start your journey towards operational excellence today!
Our industry leader
Cyber Resilience Act | Whitepaper
Cyber Resilience Act
Strengthen Your Cyber Defenses with the Cyber Resilience Act
At Siemens Advanta, we are dedicated to empowering your organization to navigate the complexities of the Cyber Resilience Act (CRA) with confidence. Our expertise in integrating cybersecurity measures ensures that you are well-equipped to protect your digital landscape.
Integrating risk management with advanced cybersecurity measures
The Cyber Resilience Act is a groundbreaking initiative that underscores the importance of cybersecurity and compliance in today’s interconnected world. It closely aligns with established frameworks such as GDPR and NIS2, providing a robust structure for digital product protection.
Our whitepaper provides a deep dive into the essential components of the CRA, highlighting the importance of integrating risk management and risk handling practices within your organization. As compliance becomes a top priority, learn how our specialized risk management services can protect your digital assets.
At Siemens Advanta, we focus on enhancing your cybersecurity and data protection efforts by guiding you towards compliance with the Cyber Resilience Act. By implementing effective risk management and network security measures, we ensure that your products and practices meet the new standards while strengthening your overall cyber resilience strategy. Embrace this opportunity to protect against threats and vulnerabilities and secure your future with our expert risk management services.
For more information, read our whitepaper on the Cyber Resilience Act.
Our industry leader
Cyber Resilience Act
Cyber Resilience Act
Product Cybersecurity Revolution – “Security by Design”
Siemens Advanta helps its clients comply with the Cyber Resilience Act by integrating Secure-by-Design principle into product development.
Siemens Advanta makes sure clients are successful in acquiring “CE Marking” and comply with the Cyber Resilience Act by integrating Secure-by-Design principles, tailoring security measures based on product criticality, and conducting risk assessments at every development stage. Siemens Advanta's proactive approach strengthens compliance and boosts its client's customer trust and market competitiveness with its secure and reliable products.
- Cyber risk assessment to identify critical risk areas and provide mitigation action items
- Product Security Program setup with appropriate levels of governance and risk-based security controls
- Proposal for post market surveillance process and team
- Provision of an outside view and cornerstone for optimization of building a secure product
- Proven approaches to develop and implement Product Security, ensuring cross-border transparency and compliance – with up to 30% less time and effort
- Reusable blueprints and trainings for further scaling within an organization
- Identify critical products containing digital elements
- Identify key stakeholders from senior management, business representatives, IT organization, manufacturing operations, and human resources
Our industry leader
Navigating Change: Manufacturing's Digital Journey
Navigating Change: Manufacturing's Digital Journey
Change is no longer just an occasional challenge for the global manufacturing industry – it has become a constant force. Today, manufacturers are facing a perfect storm of pressures that are reshaping how they operate and innovate. The industry is undergoing a seismic shift, driven by a combination of technological advances, increasing competitive pressure from emerging challengers, and global economic factors that can no longer be ignored.
Technological breakthroughs like Artificial Intelligence (AI), digital twins, and 3D manufacturing are fundamentally transforming production processes and business models. Meanwhile, new competitors are catching up fast. These upstarts are achieving near-equal levels of quality while demonstrating greater agility and innovation, making it harder for established manufacturers to maintain their edge. At the same time, labor shortages, inflation, and slowing economic growth are further compounding the complexity of operating in today’s global market.
To address these mounting challenges, manufacturing organizations are turning to the Industrial Internet of Things (IIoT) as a vital component of their strategy. IIoT offers a path forward by unlocking new efficiencies, enabling real-time insights, and creating opportunities for predictive maintenance. It helps companies do more with less. Additionally, the pressure to meet sustainability standards and increase transparency in operations only adds to the urgency to adopt IIoT solutions.
For many manufacturers, successfully leveraging IIoT is no longer optional – it is crucial to staying competitive. By deploying IIoT solutions, companies can increase operational efficiency, improve customer engagement, and gain critical business intelligence that allows for more informed decision-making. However, despite these potential gains, successfully implementing IIoT is a complex endeavor.
While some companies opt for ready-made solutions, an increasing number are developing proprietary IIoT platforms tailored to their specific needs. This approach offers numerous advantages:
- Tailored systems that integrate seamlessly with existing workflows
- Reduced reliance on third-party vendors, lowering operational costs
- The ability to refine platforms based on real-time user feedback, maximizing ROI
However, developing a bespoke IIoT solution also presents significant challenges. From integrating diverse technologies to ensuring data security and managing scalability, the road to success is paved with obstacles. Even more crucially, without a clear strategy and robust planning, companies risk turning these opportunities into pitfalls. Misaligning technology with actual work processes, underestimating the complexity of implementation, or failing to engage employees throughout the process can prevent businesses from realizing the full potential of their IIoT investments.
This is where integrated change management becomes indispensable. It’s not just about managing the technical side of IIoT deployment; it’s about aligning people, processes, and technology to ensure that the transformation delivers its intended benefits. Change management ensures that every layer of the organization – from leadership to the shop floor – embraces the shift, ultimately enabling businesses to turn challenges into competitive advantages.
Transformation and change: two sides of the same coin
Often looked at as the "soft and fluffy stuff," Change Management is also a technical discipline – reliant on fact-based research, analysis, and strategic thinking aiming at guiding an organization to sustainably introduce changes supported by the workforce. Change Management is essential for many reasons: minimizing disruptions, maximizing employee buy-in, and organizing training and development.
Bringing IIoT into any manufacturing organization requires both a shift in technology and a shift in mindset especially in relation to ‘how things were always done.’ “When organizations focus solely on the technical or operational aspects of a change initiative, they risk encountering substantial resistance and a lack of employee buy-in. This may also result in increased turnover, especially of key people.
In addition to focusing on raising awareness, acceptance and commitment of the workforce relating to changes, Change Management also works very closely with the project, or in the case of large digital transformations, the Transformation Management team. This integrated approach is essential for successful and sustainable implementation. While the Transformation Management team is planning and managing the different work streams of a project, Change Management generates valuable input for when and where those plans need to be adjusted for the organization to follow the changes and generate the expected benefits.
To sum it up, a successful Change Management program requires the acceptance of three factors:
- It is Integrated. Change Management oversees the technology and people involved in the transformation throughout the digital journey – from conception to implementation – and is connected to the Transformation Management team.
- It is Equal. Change Management is often introduced as an afterthought and is limited to communication and training measures. Doing so reduces the effectiveness of Change Management tremendously. Its contributions must be treated equally to those of project management or solution development.
- It is Iterative. Change Management anticipates and adapts to volatile and uncertain situations. “An iterative approach corresponds to developing flexible strategies and plans, and continuously adapting them while already implementing them. This contrasts with a traditional approach that would involve setting fixed goals, detailed upfront planning and rigorous implementation towards a fixed target state.
How to do it right: learn from our experiences
“The reality is that the biggest reason [I] IoT-led changes fail is the inability to reach adoption in core teams and via key stakeholders. With IoT in particular, adoption issues stem from the organizational tendency to force people and processes to accommodate a new technology rather than figure out how the tech will add value.”
A simple example is the issues that could arise if an organization forgets that there are at least five different demographic groups in the workforce right now. From the Silent Generation (1928-1945) to the Baby Boomers (1946-1964), to Generation X (1965-1980), to Generation Y/Millennials (1981-1996), to Generation Z (1997-2010) – each of these groups learn and accept technology at a different pace.
As our colleague Britta Stutzman has written, “Successful Change Management boils down to understanding and relying on the diversity of our workforce; our job is to make sure we know as best as possible what keeps our employees motivated, how they like to learn and adapt to changes and finally what makes them engage in their job.”
But how do you create a transformation program in the right way to avoid the big risk of not having buy-in from the workforce? From our own experience, there are some aspects that contribute to a successful implementation.
- Question if IoT is the right thing to do and how it helps: This might sound surprising, but what we encounter quite often is a situation where the solution is already decided, but the problem that it is supposed to solve, is still unknown. We know that everyone is eager to start and see the first features deployed, but not having clarity on why an IoT platform must be introduced and what should be achieved by it, will fall on the project’s feet later.
- Design the IoT platform based on user feedback: Allowing those affected by the change to contribute to the solution significantly reduces implementation efforts. The people who will work with the IoT platform every day know best what features they need to achieve the expected benefits. This should also not be a one-time query at the beginning, but a continuous feedback collection throughout the rollout. Every deployment of new features will generate waves of valuable input influencing the course and outcomes of the project. Highly influential individuals must be identified and engaged early to minimize change resistance and develop influential change promoters.
- Give clarity on how the IoT platform should be used: While it is always good to leave room for people to come up with their own ideas on how to make use of a solution, IoT platforms are very complex and for them to bring benefits, many different parties have to work together perfectly (e.g., to have correct data, actions can be triggered based on detected patterns). In one of our past projects, the client decided to forgo the focus groups and collaborative workshops on a new solution to let the workers show creativity in adjusting to the new tools. The workers did not have enough time to adjust to the changes causing frustration. Ultimately, the approach did not succeed, and the leaders realized that interviewing employees would provide the input to make the necessary changes.
Changing for tomorrow’s manufacturing success
Despite all the mentioned hurdles and risks associated with introducing an IoT Platform into a manufacturing setup, there is hardly a way around it for organizations that want to be prepared for the future. Fundamental changes in digitalization, automation, and demography need to be addressed proactively by any player in the manufacturing industry who strives to compete in the long run.
By opting to take the proprietary approach to IIoT, manufacturers can focus on both technology and employee acceptance of digitalization. The journey to developing a proprietary IIoT platform, despite its high investment and associated risks, underscores the necessity for strategic and early implementation of integrated Change Management. Success depends on the people within the manufacturing organization believing in, accepting, and driving the changes necessary for a full organizational transformation and manufacturing optimization.
Our contributors
34 Digital Transformation Statistics For 2024 (digital-adoption.com)
Four Key Challenges for IoT Implementation – and How You Can Overcome Them (siemens-advanta.com)
How IoT Is Transforming The Manufacturing Industry (forbes.com)
Improving Operational Efficiency with Industrial IoT: Part 1 – IIoT World (iiot-world.com)
Industrial Internet Of Things Benefits, 2024 Trends, Examples & Challenges | Matterport
IoT in Manufacturing: Applications, Technologies & Examples (itransition.com)
Key Steps to Digital Transformation in Manufacturing: Cherry Bekaert (cbh.com)
Leading the 6-Generation Workforce (hbr.org)
leveraging-industrial-iot-and-advanced-technologies-for-digital-transformation.pdf (mckinsey.com)
Making the IIoT promise real | Whitepaper | Genpact
Manufacturing Optimization – The Paradigm Shift to A Smarter System – IIoT World (iiot-world.com)
successfuldigitaltransformationwhitepaperbysiemensiotservices.pdf
Without Change Management, IoT has no chance - Software AG | Software AG
Author
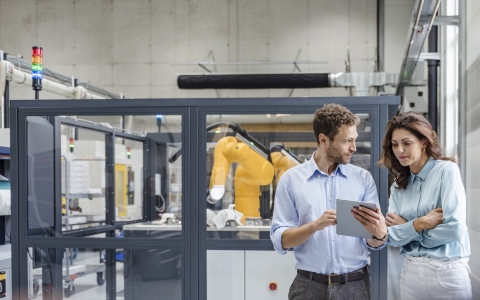
Mergers & Acquisitions (services)
Mergers and Acquisitions
M&A can transform your business, but it requires expertise throughout the process, starting in the pre-deal phase, continuing in the transaction phase, and through post-merger integration (PMI). M&A activities are often driven by a desire to increase market share, expand product lines, or gain access to new markets. Successful M&A transactions require careful planning, due diligence, and effective execution to achieve desired outcomes and create value for stakeholders - something we have proven time and again at Siemens Advanta.
- Identify the appropriate M&A prospect
- Evaluate the advantages and disadvantages of a possible acquisition
- Develop the integration plan, discover potential synergies, and guarantee preparedness from Day 1
- Achieve faster growth
- Facilitate the transfer of technology
- Accomplish diversification
- Attain positive synergy
- Increase market power
Our industry leader
Compliance with EU Data Act
Compliance with EU Data Act
EU Data Act: Prepare for New Regulations
To foster the data economy in the European Union, EU legislators are currently reshaping business ground with new laws that shall enable fair and simple access to and use of data. The latest legislation: the EU Data Act, will become effective in September 2025.
With this deadline on the horizon, manufacturers of connected devices and others are required to act now. The timeline is tight, the obligations and requirements are ambiguous and fundamental business questions need to be clarified.
What is EU Data Act?
One important aspect of the EU Data Act is to grant users of connected products the right to access the generated machine data. In addition, the Data Act allows users to grant access to that data to third parties, which may be, for instance, independent service providers, AI startups and potentially also competitors.
Users and third parties may use the data for their own purposes, including providing third party service (as an alternative to manufacturer provided services) or analytics offers.
Manufacturers that fail to provide data access risk facing substantial financial penalties. The penalties shall be effective, proportionate and dissuasive and may have retroactive effect; if personal data is concerned, fines shall be according to the GDPR, which means the higher of EUR 20 million or 4% of the annual global revenue.
What is required and when?
Beside other obligations, manufacturers of connected products need to fulfill three key obligations by two deadlines.
- Information obligation
Starting from September 2025, manufacturers of connected products are required to inform users at point of sales about the data that the connected product generates during usage.
- Data sharing obligation
Starting from September 2025, the data holder (usually the manufacturer, if it chooses to collect the machine data) is required to share available data with the user of the connected product as well as with third parties authorized by the user.
- Design obligation
One year later, starting from September 2026, manufacturers must design new products in a way that the data is directly accessible to the user.
What do these obligations imply? Companies that sell connected products need to react now and start designing and implementing response strategies for sharing the relevant data. Yet, as is often the case, the details are where the real challenges lie.
Who does the law apply to?
The above-mentioned obligations under the EU Data Act apply to all manufacturers of connected products that make their products available in the EU, irrespective of their industry and place of establishment.
The right to access data is restricted to users within the EU. Third parties that were granted access by users must have a legal representation in the EU to be eligible for data access.
How can you become compliant?
The path to compliance is individual for each company, yet there are four key tips, from our experience, to make the journey a smoother one.
- Setting up a cross-functional team
Due to the complexity of this topic, different functions and experts from within the clients’ organization and from external need to be mobilized, including legal, government affairs, R&D, product management and IT. It is advised to involve all experts and concerned business units from day 1 to form a joint response strategy moving forward.
- 80/20 and risk-based approach
The Data Act applies not only to new products, but also to the existing installed base in many cases. Companies with a large variety of product families need to carefully plan their approach to balance the need of being compliant and the effort to implement.
- Close collaboration between legal and technology experts
Companies usually need to develop a new technical solution to fulfill the obligations under the Data Act. It is neither a pure technical nor an entire legal decision. Technical feasibility/effort and legal compliance risks need to be evaluated jointly to come up with an optimal solution. In addition, sales and customer service teams need to be involved as well to ensure a smooth customer experience.
- Treat this as a business opportunity rather than a pure compliance burden
Despite being a compliance topic from the first glance, the EU Data Act also provides vast opportunities for companies to capture. Creating new revenue streams of providing data, offering third party maintenance services for other companies’ products, or conducting AI analytics on competitors’ machine data, the opportunities seem endless.
How can Siemens Advanta help?
With our footprint in various industries and specifically our experience with the EU Data Act, we can support our clients on their way to become compliant with the obligations. Our project management services span from hands-on project management office support for urgent content issues, to developing comprehensive data strategies designed to meet future digital challenges. Siemens Advanta tailors its offerings and strategies to align with the unique needs and stages of development in areas, e.g. system architecture and data literacy, ensuring that our services are well-suited to each client's specific circumstances and objectives.
If you want to learn more about our offerings regarding the EU Data Act, please download the detailed presentation on the topic here:
Industry experts
Disclaimer
The information provided herein is for general informational and promotional purposes only and may not be accurate, complete or up to date. The information does not constitute any regulatory, legal, financial, technical or other professional advice.
No responsibility or liability will be accepted for any errors, omissions or inaccuracies in the content. Siemens Advanta disclaims, to the fullest extent permitted by applicable law, any and all liability or responsibility for the accuracy and completeness of the information contained herein and for any acts or omissions made based on such information. Siemens Advanta does not provide any legal, regulatory, audit, or tax advice; readers are responsible for obtaining such advice from their own legal counsel or other licensed professionals.
Cloud Solution improves data transparency leading to higher utilization and efficiency
Cloud Solution improves data transparency leading to higher utilization and efficiency
Swire Coca-Cola Limited is the fifth largest bottling partner of The Coca-Cola Company by global volume with a franchise to manufacture, market and distribute products of The Coca-Cola Company in Greater China, Cambodia, Vietnam and the western USA.
Swire Coca-Cola China faced limitations in data analysis due to a lack of comprehensive data, restricted KPIs, and inefficient manual data collection in production.
Cloud architecture enabled configurable and automatic data acquisition, multi-dimensional KPI aggregation, and data transparency on mobile phones
Together with Siemens DI edge solution, cloud solution has improved customer USLE (Unconstrained System Line Efficiency) by 4.2% since 2021 and throned China #1 USLE region in 2022 among all Coca Cola markets.
Dive deeper: Related content
Our industry leader
Spend Analytics
Spend Analytics
Vendigital as part of the Siemens Advanta organization, drives accelerated cost transformation through data.
We consolidate and transform low integrity data from disparate ERP/MRP systems into valuable business intelligence which helps drive rapid cost, cash and efficiency improvement across your organization. This is delivered through our secure, cloud-based portal environment.
Designed by purchasing professionals for purchasing professionals, Spend Analytics provides instant access to valuable business intelligence, drives efficiencies, and accelerates business performance. It offers a powerful, highly intuitive means of placing spend information at the client’s fingertips, through a user-friendly, customizable interface. Delivered as a managed service through our secure portal environment, Spend Analytics enriches the outputs of traditional ERP and MRP systems and provides instant answers to those procurement questions you just haven’t be able to reach.
- Smart data processing technology combined with human intelligence providing data integrity you can rely on.
- Unparalleled insights within complex supply chains, allowing you to drill down to the cause in seconds.
- Empower your teams with the tools that allow them to make better decisions, faster.
- Macro-to-micro drill down by site, supplier, category and many more.
- Transaction-level direct & indirect material analysis and deep insights.
- Visualisation of key strategic and operational procurement metrics that allow you to take action in confidence.
- Eliminate the need for ongoing data manipulation freeing up time your teams to take action.
Our industry leader
Supplier Analytics
Supplier Analytics
Vendigital as part of the Siemens Advanta organization, drives accelerated cost and supply chain performance transformation through data.
We consolidate and transform low integrity data from disparate ERP/MRP systems into valuable business intelligence allowing you to better collaborate with your supply chain in order to drive sustained cost, quality and delivery performance improvement, all delivered through our secure, cloud-based portal environment.
Our Supplier Analytics application enables our clients to quickly analyze and track quality, cost and delivery (QCD) performance across the organization, as well as invite suppliers to assess and challenge their performance allowing both parties to work collaboratively to drive improvement based on a single source of truth.
- Measure and analyze QCD performance across the organization based on a common standard so as to ensure like-for-like comparison.
- Issue scorecards to suppliers and allow them to challenge in order to improve data integrity and collaboration to drive performance improvement.
- Macro – micro analysis to quick establish root cause.
- Reason code analysis to understand common themes driving poor performance.
- Track supplier engagement to facilitate targeted communication.
- Analyze and track QCD performance across the business.
- Macro-to-micro analysis allowing you to get to the root cause.
- Facilitates boardroom engagement and input to the strategic direction.
- Enable fact-based conversations with suppliers on areas for improvement.
Our industry leader
Pagination
- Page 1
- Next page